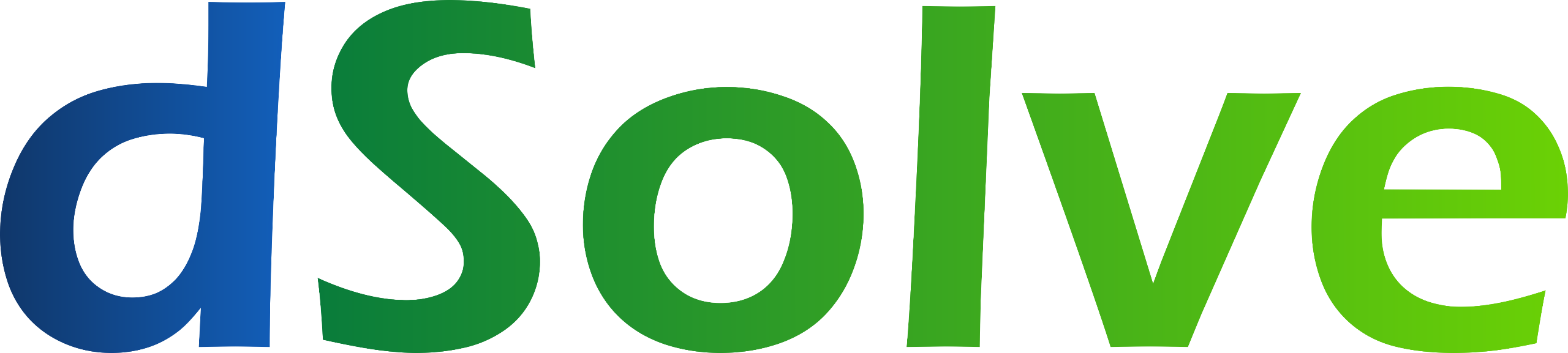
dSolving Plug & Abandonment cost and emissions
About the company
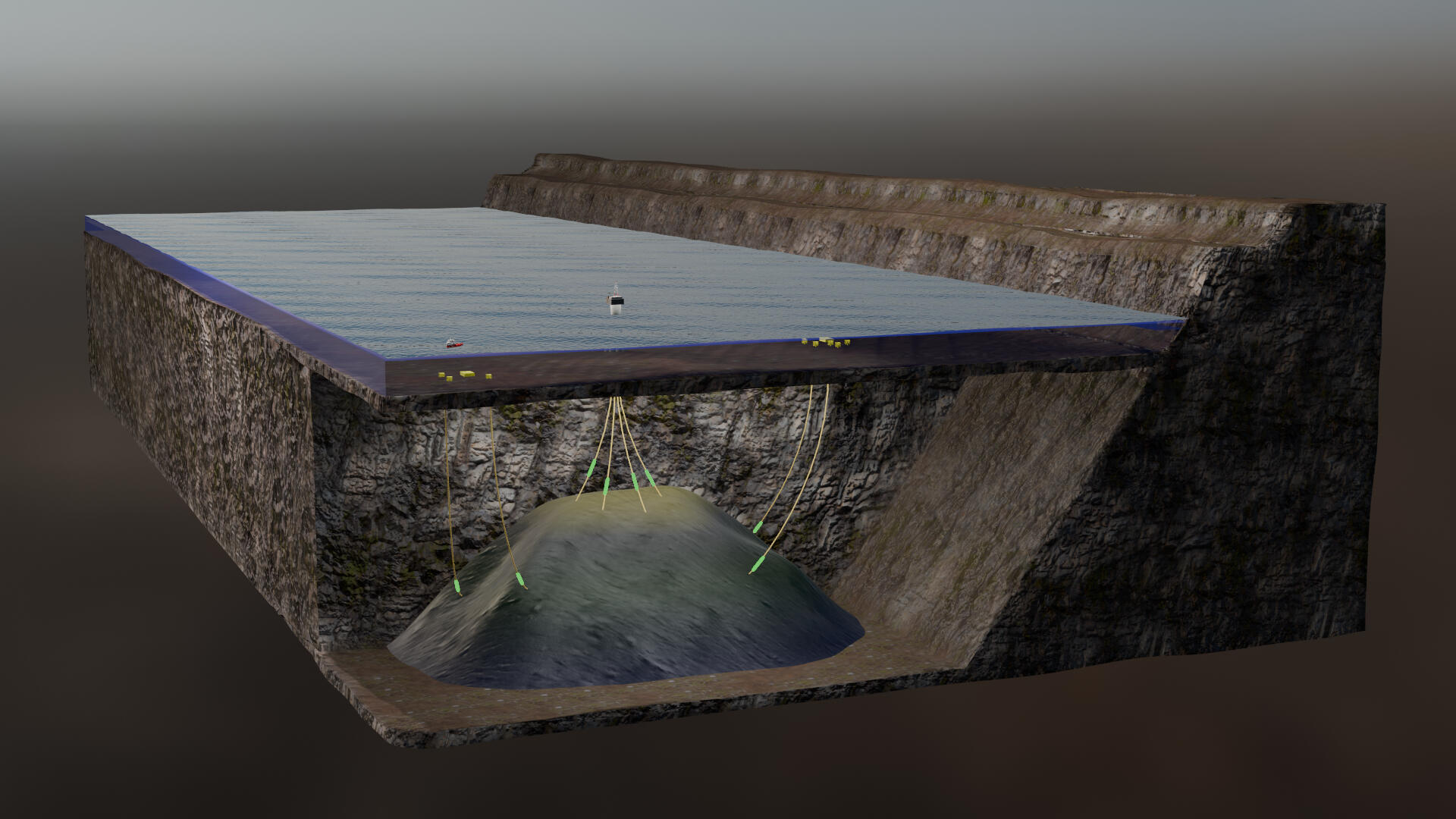
dSolve AS is a startup based in Trondheim, Norway, with the vision to pioneer rigless plugging & abandonment and well intervention.Its current mission is to develop a commercial wireline tool to open windows in casing for plugging & abandonment of wells without using a rig.The dSolve team has been developing the innovation since early 2016. It started as a research project driven by dSolve AS, together with SINTEF, industry partners and with support from Norwegian innovation support institutions. After the successful concept validation, the Research Council of Norway funded further research that resulted in the successful validation in relevant environment.Thanks to the support from Oil Industry Partners and the Research Council of Norway, dSolve started the ongoing Joint Industry Project in mid-2023 aimed at developing a downhole wireline prototype for field testing.
The Concept
Electrolysis
The dSolve concept is based on using an electrical current to stimulate a non-spontaneous reaction in order to dissolve a metal into a solution.This process is performed by using an electrochemical cell, which consists of an external power supply, two electrodes (anode and cathode) and a conductive solution or brine. This conductive brine is usually present in the well to be plugged and abandoned.
The electrochemical reactions cause the iron present in the casing or tubing to dissolve anodically while hydrogen gas evolves cathodically. The dissolved iron ions react with hydroxide ions in the conductive brine and precipitate as Iron Hydroxide, while excess iron, sodium and chloride ions will stay in the solution.
Tool description
The dSolve concept will be realized as a wireline tool that consists of:-A long cathode or conductive element-A downhole power supply that provides the electrical current required for the electrolytic process.-A clamp that makes an electrical connection between the casing and the tool-Telemetry and control-And a cable head and a standard wireline
dSolve operation
The dSolve tool is first placed where the window is required, the downhole power supply is activated, and the dissolution of the metal tubing begins.During this process, the iron separates from the tubing until the metal surrounding the cathode is dissolved into the solution. The tool is then moved to the next position and the process continues until the required window length is opened.With further development the process could be performed to open windows in multiple size casing.
Features and benefits
Benefits to the environment
The dSolve tool is being developed to be operated with a standard wireline unit. This is possible due to the state of the art downhole electronics that minimizes the energy consumption during the transfer of power to the the downhole electrolytic cell.While the emissions from a typical 16 M Watts drilling rig averages 200 tons per day, the CO2 emissions by dSolve and other equipment required for the operation is estimated at 4.5 tons per day. It is estimated that a dSolve could reduce up to 80% CO2 emission compared to performing similar operations with a drilling rig.In addition, there will also be reductions in emissions related to maintaining a big rig crew offshore and the crew mobilization to and from the rig.
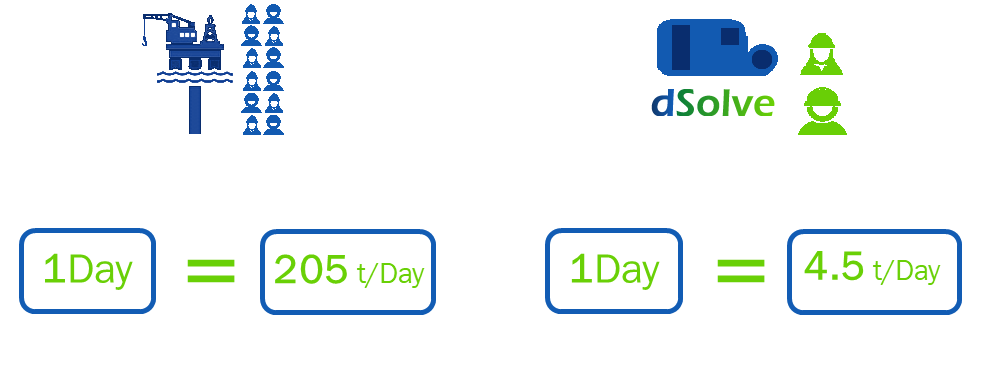
Compatible with existing equipment
The ongoing development is aimed at engineering and manufacturing a downhole tool that can be operated with industry standard wireline equipment such as surface power supply and wireline.
Verifiable results
An important industry requirement is that the opening of the cross-sectional window can be verified before the barrier is placed.As the dSolve process is controlled and monitored from the surface, dSolve personnel can identify when the metal surrounding the cathode has been dissolved and the window has been fully opened.
Versatile operation
Results from the laboratory have demonstrated that casing and tubing can be dissolved at any inclination.Other experiments performed together with SINTEF have also confirmed that the process works with tubing with L80, 13Cr-L80, P110 and Q125 grades.
Safe to operate
By using standard wireline equipment and existing brines as electrolyte, the dSolve concept does not introduce any new hazardous procedures, equipment or chemicals to the operation.
Our ambitions
In addition to P&A, our ambitions include revolutionizing other well intervention operations with many potential applications waiting to be explored. Some of these applications include a wireline whipstock assembly that would enable opening casing exits for sidetracking without the use of a milling BHA, coil tubing or a drilling rig.
dTrack - Wireline Whipstock Assembly
dTrack is a concept based on the dSolve technology and its capabilities to dissolve iron from focused areas of the tubing.
Tool description
dTrack is a wireline tool that combines a whipstock assembly, that includes a fit for purpose anchor, together with an enhanced dSolve tool with a cathode shaped to fit the face of the whipstock.
dTrack Operation
The dTrack tool is placed where the casing exit is required. Once the anchor is locked, the face of the whipstock with the fitted cathode is oriented towards the required direction for the sidetrack.The dSolve downhole power supply is activated, and the dissolution of the metal tubing begins.During this process, the iron adjacent to the oriented cathode separates from the tubing until the metal surrounding the cathode is dissolved into the solution, while the section of tubing behind the whipstock remains unaffected.Once the oriented casing exit is opened, the cathode is disconnected from the whipstock. The cathode together with the rest of the components of the dSolve tool is then pulled out of the hole, leaving the whipstock anchored, and the exposed formation ready to be drilled.
Features & Benefits
-The rigless concept can be deployed with a wireline or coil tubing unit-As a milling BHA is not required to open the oriented window, troublesome metal swarf is not produced and the rathole is not drilled-The size and shape of the oriented window depends on the shape of the cathode. Therefore, the window can be optimized to safely run Rotary Steerable Systems or any drilling BHA-In conditions when the sidetrack is to be performed in relative soft formations, the whipstock could be made with softer materials more friendly to the drilling BHA / bit
Supporting experimental results
With support from the industry partners, the dSolve team performed experiments that demonstrated the capabilities to dissolve iron from focused areas of the tubing.During these experiments a cathode was modified to expose only an oriented section to an L-80 4.5" tubing.As shown in the pictures below, an oriented casing exit was opened in the metal tubing. Furthermore, the opening of the oriented casing exit is similar in shape to the exposed cathode, demonstrating the feasibility of the dTrack concept.